The manufacturing industry has undergone a dramatic transformation over the past few decades, with one of the most impactful advancements being the integration of robotics and automation into production processes. As companies strive for greater productivity, precision, and cost-effectiveness, robotics has become an essential tool in modern manufacturing. However, successfully incorporating robotics into an existing system is far from a simple plug-and-play process. It demands meticulous planning, strategic design, and expert implementation. This is where servo products company can help.
The following article explores the role of automation integrators in the process of robotics integration in manufacturing, the benefits in manufacturing, and the key considerations businesses must take into account when adopting these technologies.
What Are Automation Integrators?
Automation integrators are specialized firms or consultants that provide expertise in the design, implementation, and maintenance of automated systems, including robotics, in various industries, including manufacturing. These integrators serve as the bridge between manufacturers and the complex automation technology required to enhance operations.
They work closely with manufacturers to assess their needs, develop tailored solutions, integrate robotics and other automation technologies, and ensure smooth system operation. Their role extends beyond the initial implementation phase, as they also provide ongoing support, maintenance, and optimization to ensure long-term success.
Integrators have expertise in a variety of areas, including:
System design: Crafting automation solutions based on the specific needs and objectives of a manufacturer’s operations.
Robotics integration: Selecting and implementing the right robotic systems to handle specific manufacturing tasks, whether it’s assembly, welding, packaging, or inspection.
Software development: Developing and integrating control software to manage robotic systems and coordinate them with other manufacturing processes.
Testing and validation: Ensuring that the newly integrated robotics systems function correctly and meet the performance standards required for manufacturing success.
Training: Providing training for operators and other personnel to effectively work with the new systems and technology.
The Role of Robotics in Manufacturing
Robots have long been a part of the manufacturing landscape, particularly in industries like automotive and electronics. However, as robotics technology has advanced, the capabilities and applications of robots in manufacturing have expanded significantly. Robotics in manufacturing can take several forms, including:
Industrial Robots: These are the large robotic arms used in tasks such as assembly, material handling, welding, and painting. They are highly versatile and can be programmed to perform a wide range of functions in the manufacturing process.
Collaborative Robots (Cobots): Unlike traditional industrial robots, which operate autonomously, cobots are designed to work alongside human workers. These robots are equipped with sensors and safety features to ensure they can collaborate safely in close proximity to humans. Cobots are commonly used in industries where human dexterity and robot precision need to complement each other.
Mobile Robots: Automated Guided Vehicles (AGVs) and Autonomous Mobile Robots (AMRs) are used for material transport in manufacturing facilities. These robots can move raw materials, parts, and finished products between different areas of the factory floor without the need for human intervention.
Robotic Process Automation (RPA): This type of automation uses software robots to perform repetitive administrative tasks, such as data entry, inventory management, and quality control, freeing up human workers for more strategic functions.
The use of robots in manufacturing offers numerous benefits, which is why so many companies are making the investment in automation technology.
Benefits of Robotics in Manufacturing
Increased Productivity
One of the most significant benefits of integrating robotics into manufacturing is the increase in productivity. Robots can work around the clock without the need for breaks, sleep, or vacation time, allowing manufacturing operations to run continuously and at a faster rate than human workers. Additionally, robots can handle repetitive, monotonous tasks with greater speed and efficiency, helping to eliminate bottlenecks in the production line.
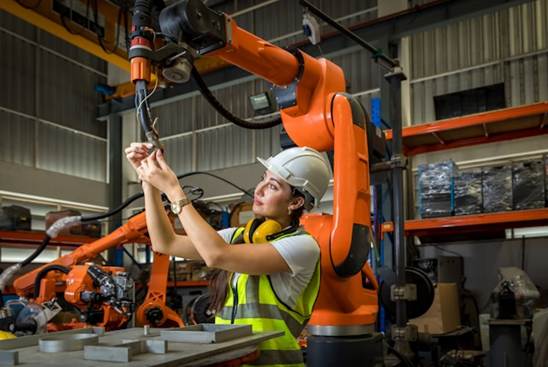
Improved Precision and Consistency
Robots excel at performing tasks with precision and consistency. Whether it’s assembling parts, welding, or packaging, robots can complete these tasks with high accuracy, reducing the chances of defects and ensuring that products meet stringent quality standards. In industries like electronics or aerospace, where small margins of error can lead to expensive mistakes, robotic precision is particularly valuable.
Cost Savings
While the initial investment in robotics can be significant, it is often offset by long-term cost savings. Robots help to reduce labor costs by performing tasks that would otherwise require human workers. Moreover, robots reduce the risk of errors and product defects, which can be costly to fix. Over time, the savings in labor costs and improved quality can make the investment in robotics more than worthwhile.
Enhanced Safety
Robots can take on dangerous tasks that are unsafe for humans, such as handling toxic chemicals, working in high-temperature environments, or lifting heavy objects. By automating these tasks, robots help reduce workplace injuries and improve overall safety on the factory floor. Additionally, collaborative robots (cobots) are designed to work alongside human workers safely, providing support without the risk of injury.
Flexibility
Robots can be easily reprogrammed and adapted to different tasks, which adds flexibility to the manufacturing process. This is particularly useful in industries that require frequent product changes or small-batch production. With robotic automation, manufacturers can quickly adjust their processes without incurring high costs, making them more adaptable to changing market demands.
Key Considerations
While robotics can bring significant benefits, there are important considerations to take into account when integrating robotics into a manufacturing environment. Automation integrators are instrumental in addressing these challenges, but manufacturers must be proactive in planning and managing the integration process.
Assessing Needs and Selecting the Right Robotics Systems
The first step in integrating robotics is identifying the specific tasks that need automation and selecting the right robotic systems for those tasks. There are many types of robots, each suited to different applications, and choosing the wrong robot can result in inefficiencies or increased costs. Automation integrators work closely with manufacturers to assess needs and recommend the best robotics solutions based on production goals, space constraints, and cost considerations.
System Integration
Robotics must be seamlessly integrated into existing manufacturing systems, including machinery, conveyors, and inventory management systems. Ensuring compatibility and coordination between robots and other manufacturing components is critical for maintaining efficiency and minimizing disruptions to production. Automation integrators manage the complex task of integrating new robotics systems with existing systems to ensure smooth operation.
Training and Support
Proper training for operators and other staff is essential to ensure that robots are used effectively. Operators must understand how to monitor, troubleshoot, and maintain robots to ensure continuous operation. Additionally, ongoing support and maintenance are necessary to keep robots performing at peak efficiency and to address any potential issues before they result in costly downtime.
Cost and Return on Investment (ROI)
Integrating robotics into manufacturing requires a significant financial investment. Manufacturers must carefully calculate the expected ROI from automation, factoring in the cost of purchasing and installing robotics systems, training employees, and maintaining equipment. Automation integrators help assess the long-term benefits and provide guidance on the financial feasibility of implementing robotics.
Conclusion
The integration of robotics into manufacturing is no longer just a futuristic concept; it’s a reality that has the power to revolutionize industries. Robotics offers benefits such as increased productivity, improved precision, cost savings, and enhanced safety. However, the integration of robotics requires careful planning, expertise, and system integration, which is where automation integrators come in. By working with these professionals, manufacturers can optimize their operations, increase their competitive advantage, and reap the many benefits that robotics brings to the table. Whether it’s selecting the right robots, ensuring system compatibility, or providing training and support, automation integrators play an essential role in helping manufacturers fully realize the potential of robotics in their operations.