Declan Birmingham works as a welder and fabricator in Dekalb. In the following article, Declan Birmingham of Dekalb delves into the multifaceted role of welding across various sectors, shedding light on its applications, techniques, and significance in driving innovation and progress.
Welding is the cornerstone of manufacturing and construction, serving as the backbone of numerous industries worldwide. Its versatility and indispensability make it a fundamental process in creating structures, machinery, vehicles, and more.
Declan Birmingham of Dekalb Explores Welding Across Verticals
Automotive & Aerospace Manufacturing
The manufacturing sector relies heavily on welding processes, each with its unique applications and requirements. In automotive manufacturing, welding techniques like MIG (Metal Inert Gas) and spot welding play a crucial role in assembling vehicle frames, chassis, and body panels, ensuring structural integrity and durability.
Similarly, the aerospace industry utilizes specialized methods such as TIG (Tungsten Inert Gas) welding to fabricate aircraft components like fuselages, engine parts, and landing gear, where precision and strength are paramount.
Electronics & Construction
Declan Birmingham of Dekalb explains that in the electronics manufacturing sector, micro-welding is employed to join tiny electronic components on circuit boards with precision, enabling the production of intricate electronic devices.
Additionally, structural welding is fundamental in constructing steel and metal structures, including bridges, skyscrapers, and commercial buildings. Declan Birmingham of Dekalb explains that welders use techniques like arc welding to join structural steel components, such as beams, columns, and trusses, forming the framework of large-scale structures. Welded connections provide strength and stability to the entire structure, enabling it to withstand the forces of gravity, wind, and seismic activity.
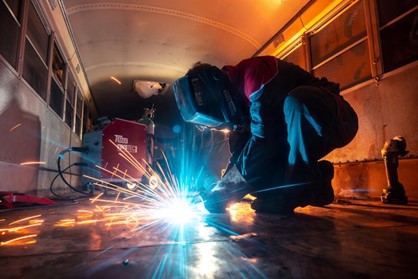
Pipeline Welding
Pipeline welding is another vital application of welding in the construction industry, particularly in the transportation of oil, gas, and water. Declan Birmingham of Dekalb says that the quality of welds is crucial in pipeline construction to prevent environmental contamination, ensure efficient fluid transport, and maintain the integrity of the pipeline system over its operational lifespan.
Infrastructure
Moreover, welding plays a significant role in infrastructure projects, including roadways, railways, and tunnels, where welded connections provide stability and strength to the structures. Declan Birmingham of Dekalb notes that common materials like steel are preferred for their strength, versatility, and affordability across various industries, while aluminum welding presents challenges due to its lightweight nature and is widely used in aerospace, automotive, and marine applications.
Measuring Quality Control
Quality control measures such as non-destructive testing (NDT) techniques including ultrasonic testing and radiographic inspection are implemented to detect weld defects and ensure compliance with industry standards. Additionally, training and certification programs play a crucial role in maintaining high standards of craftsmanship and competency, ensuring that these skilled laborers possess the necessary skills and knowledge to perform their tasks safely and effectively across diverse industrial settings.
Common Welding Materials and Techniques
Steel Welding
Declan Birmingham of Dekalb explains that steel welding is prevalent due to the material’s strength, versatility, and affordability, making it suitable for various applications across industries. From structural steel in construction to automotive components and machinery parts, steel welding is essential for fabricating and joining metal structures and components.
Aluminum Welding
Welding aluminum presents unique challenges due to its low melting point, high thermal conductivity, and susceptibility to heat distortion and oxidation. Specialized techniques with aluminum-specific wire and shielding gas are commonly used to overcome these challenges. Aluminum welding finds widespread use in aerospace, automotive, and marine applications due to the metal’s lightweight properties and corrosion resistance.
Advanced Welding Methods
Laser and electron beam welding are cutting-edge technologies known for their high precision and suitability for specialized applications.
Laser welding utilizes a concentrated laser beam to melt and join metals with minimal heat-affected zones, making it ideal for welding thin and delicate materials in industries like electronics, medical devices, and automotive manufacturing.
Electron beam welding, on the other hand, uses a focused beam of high-velocity electrons to achieve deep penetration welds in thick materials with minimal distortion, making it suitable for aerospace, defense, and nuclear industries. These advanced welding methods offer superior accuracy, control, and efficiency compared to traditional welding techniques, enabling manufacturers to achieve high-quality welds in complex components and assemblies.
Conclusion
Welding serves as the linchpin of modern manufacturing and construction industries, enabling the creation of intricate structures and machinery that drive global economies forward. As technology advances and industries evolve, the demand for skilled welders and innovative welding techniques continues to grow, underscoring the enduring importance of welding in shaping the world around us.